MEDICAL CASTINGS
WE HAVE GROWN TO BE ONE OF THE MAJOR SUPPLIERS OF MEDICAL INVESTMENT CASTINGS IN THE USA, WITH A 35,000 SQUARE FOOT FOUNDRY IN WARSAW, INDIANA PROVIDING THE BULK OF OUR CASTINGS.
We can also provide castings from our secondary foundry located in India, which can be beneficial for larger runs and even cost management. In-fact, in total, our ISO-certified manufacturing plants across the world exceed 200,000 sq.ft.
Together it provides our customers with unrivaled lead times, capacity, and quality.
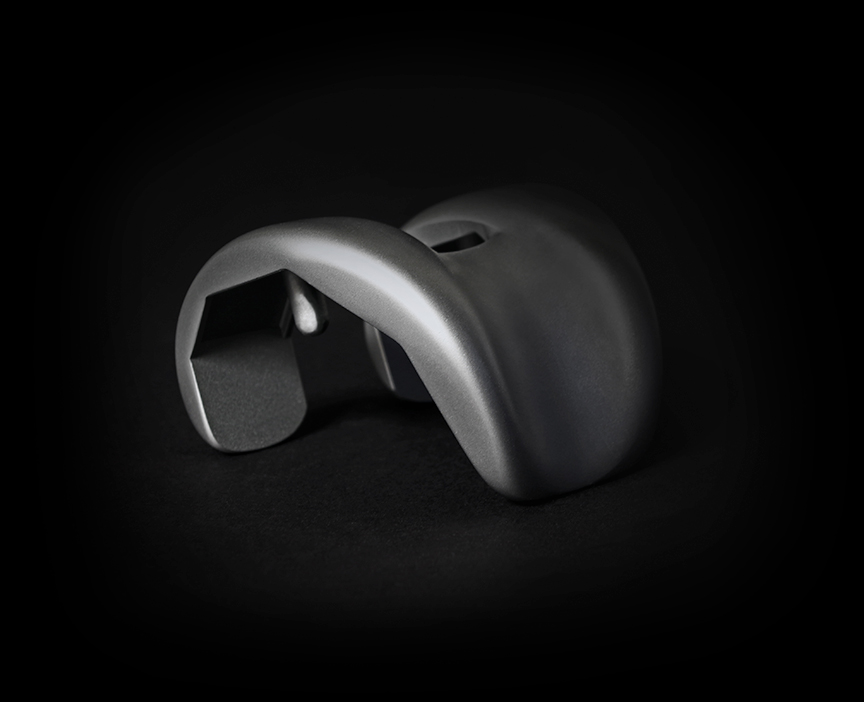
“PROVIDING BOTH PROTOTYPES AND PRODUCTION SAMPLES PHENOMENALLY BELOW INDUSTRY STANDARD LEAD TIMES ENABLED US TO LAUNCH OUR PRODUCT INTO THE MARKET MUCH SOONER THAN ORIGINALLY PLANNED”
The bulk of our medical castings are for the orthopedic industry, whom we supply with precision cast hips and knees. Other areas we cast for the medical industry are:
- X Ray Equipment.
- Vital scanning equipment.
- Blood Analysis equipment.
Materials
We commonly cast all of the metal alloys found in the market today, along with an increasing track record of exploring and delivering the casting of previously uncastable materials.
Most commonly used in our orthopedic investment castings are cobalt chrome and stainless steel, and we can finish these within the USA.
For a full list of our investment casting materials, see our page here.
OUR MANUFACTURING PLANTS IN THE US AND INDIA MEANS UNRIVALLED CAPACITY AND ULTRA QUICK LEAD TIMES.PUT US TO THE TEST TODAY.
OUR BENEFITS
CASTING
We cast in air with an inert shield and use either tilt furnaces or rollover furnaces.
COBALT CHROME
We source our Cobalt Chrome locally, from vendors approved by the most significant orthopedic companies in the world.
13485 CERTIFIED
Texmo Precision Castings is ISO 13485 certified. Both US and India facilities are qualified to supply to high-end medical device companies.
100% GUARANTEE
The material is checked upon cast to 100% guarantee and certifies that we meet the material specification every single time.
ON-SITE TESTING
All non-destructive testing is carried out on-site, thus allowing low costs to the customer and rapid turnaround.
FAST LEAD TIMES
Outside processing vendors are situated within the same vicinity, and therefore lead-times are slashed – 4 weeks is our standard for stem components.
TRACEABILITY
Traceability is our strong point, and our systems and procedures allow us to record manufacturing steps from wax injection to shipping.
ORGANISE A CHAT WITH ANDY
[contact-form-7 404 "Not Found"]